Innovative solutions for reducing temperatures in SCHOTT’s production halls
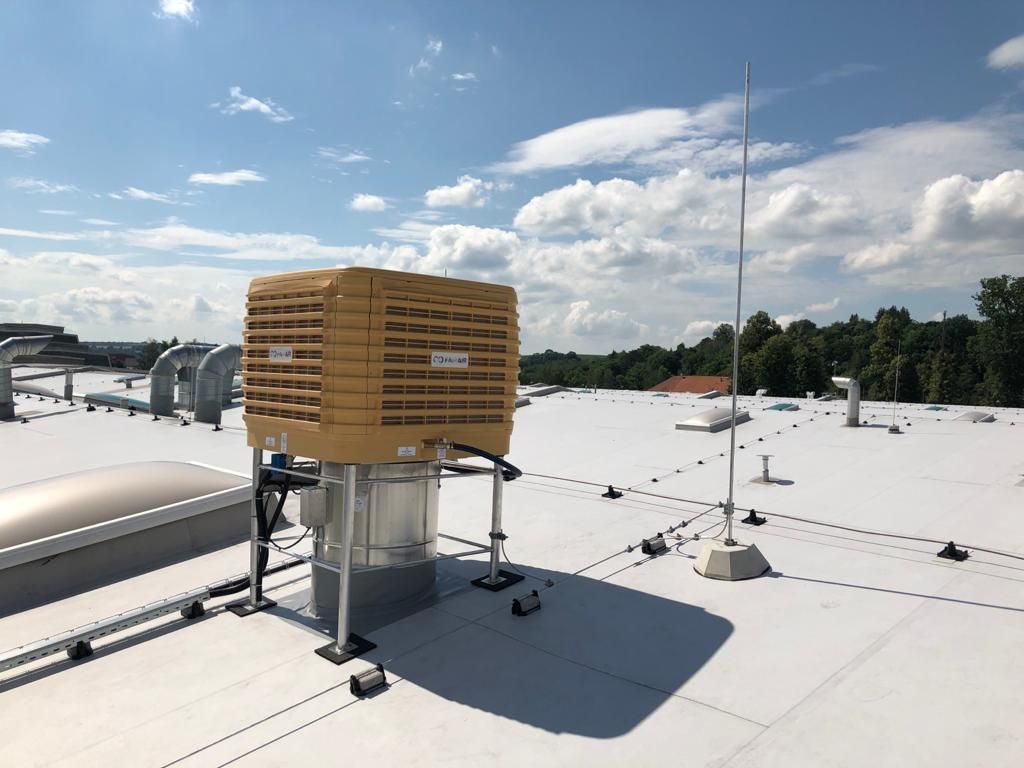
SCHOTT Electronic Packaging Lanškroun s.r.o. was established in March 1993 thanks to a collaboration between Tesla Lanškroun a.s. and SCHOTT Landshut from Germany. The company specializes in hermetic packaging solutions that utilize advanced glass-to-metal sealing technologies.
Over the past two decades, the plant in Lanškroun has become a key center for producing components for the automotive industry, while also supplying innovative solutions in optoelectronics and other specialized applications.
SCHOTT Installation in May 2020
SCHOTT faced the challenge of improving temperature conditions and comfort in its production hall, where employees suffered from high temperatures affecting their comfort and productivity. Our goal was to reduce the temperature in the working zones and create a more pleasant and stable work environment.
Project specifics:
The project was carried out during the summer months when temperatures inside the hall reached critical levels, causing frequent overheating of production equipment and discomfort for workers. The challenge was to install a cooling system without interrupting the production process.
Technology used:
For this project, we installed 2 FAIRAIR adiabatic cooling units. These units work on the principle of evaporative cooling, naturally lowering air temperatures while also ensuring the circulation of fresh air. This solution enabled a fast and efficient reduction in hall temperatures without the need for extensive structural modifications.
Result:
After installation, the hall temperature was reduced by 5 °C, significantly improving working conditions. Employees appreciated the improved air quality and the reduction of heat-induced fatigue. This solution also contributed to greater production efficiency as equipment was no longer exposed to excessive heat, preventing downtime.
SCHOTT Installation in December 2020
The second project for SCHOTT took place under more challenging winter conditions, where we faced extremely low outdoor temperatures and snowfall. Our goal was to address the cooling and ventilation needs of the production zones, adapting the installation of technological elements to the weather.
Project specifics:
The project was carried out during winter, with roofs covered in snow. Despite these challenges, we successfully completed the installation, which required coordination between multiple technical teams. The working environment in the production halls was segmented, requiring individual solutions for each work zone.
Technology used:
For this project, we installed 5 FAIRAIR adiabatic evaporators, which provided cooling and improved air quality at various workstations. As part of the project, we also supplied different types of directional air outlets, adapting the airflow to the specific needs of individual work zones. In addition, we installed 5 FAIRAIR extraction units to remove heat load and VOCs (volatile organic compounds generated during the production process).
Energy balance:
The total energy consumption for both projects reached 8.9 kW, with the hall volume being 35,000 m³. This solution ensured effective ventilation and cooling of the entire production space.
Result:
The temperature in the production hall decreased by 6 °C, significantly improving the working environment for employees. Improved air quality and circulation contributed to reduced production downtime, as equipment was no longer exposed to excessive overheating.
This project also demonstrated our ability to work in extreme conditions, as we successfully completed the installation despite adverse winter weather.