Better air for Continental Barum
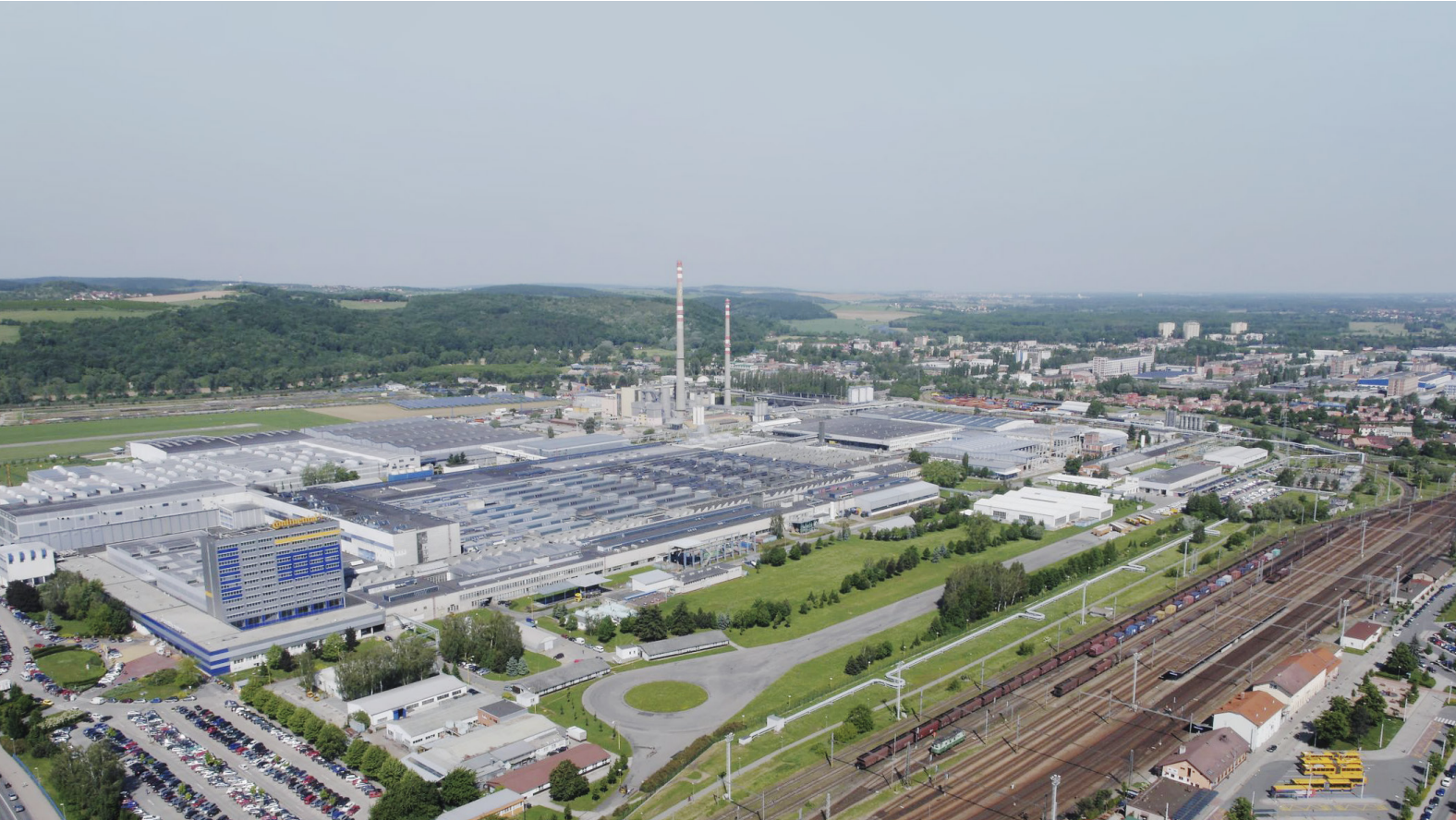
Continental Barum s.r.o., based in Otrokovice, is the largest European tire manufacturer for all types of vehicles. Rubber manufacturing has a longstanding tradition in the region, beginning in 1932 with Tomáš Baťa, who started producing truck tires for vehicles transporting his shoe products throughout the country and beyond. In 1972, a tire plant was officially opened in nearby Otrokovice, now employing over 5,000 people. This industrial site produces over 21 million passenger and light truck tires and nearly 1.4 million truck and industrial tires annually.
What was the condition of the site?
This 55-year-old, energy-inefficient building spans 35 hectares and is divided into an external part, an internal part, and a connecting corridor. The roof is flat, made of concrete monolithic panels with an older type of roof membrane. The roof includes large shed skylights, a source of heat gain for the building. During ongoing renovations, some of these areas have been fitted with sandwich panel roofing, while the unrenovated sections have thermal insulation panels made of chipboard with a roof membrane surface. The side sections of renovated skylights are filled with glass copilit, while unrenovated ones still use the original wired glass.
FOUR PROJECTS IMPLEMENTED FOR BARUM
2018: PILOT INSTALLATION PROJECT
Location: Tread assembly – layering tire components, pre-preparation for vulcanization (final fusing and tread molding). Open space in close proximity to the press area.
Project Specifics: Building’s structural constraints. No possibility of roof installation. Complex structure of roof trusses. Dense layout of production equipment. Immediate proximity to the press area, which generates: 1) extreme heat load, 2) airborne oil aerosol and other pollutants due to vulcanization, and 3) intense odor. Localized cooling without additional structural modifications risked warm, polluted air flowing into the treated area, impacting measured results. The budget limit was predefined.
Goal: The pilot project aimed to test the functionality and efficiency of the FAIRAIR system with a target to lower the temperature by at least 5°C while maintaining relative humidity below 60%, as required by the production process.
Technology Used: Four units of adiabatic evaporators (FAEV601) for cooling, four heat extractors (FAEP900) to reduce temperature by extracting heat, four HVLS destratifiers (FADS400WD) to improve circulation, lower perceived temperature, and save on heating in winter, and four misting units (FAHUUX) to shield the area from heat pulled from the press area and remaining open spaces. Total energy balance: 15 kW; air exchange rate: 5x per hour.
Result: Temperature reduction of 6.6°C while maintaining relative humidity at 55%.
2019: COMPLETION OF THE ENTIRE TREAD ASSEMBLY AREA
The pilot installation met expectations, and limited funds allowed further installation of destratification units throughout the tread assembly area. The project's goal was to improve working conditions for both machinery and staff by increasing air circulation and reducing the impact of high temperatures, which led to excessive sweating and damp clothing.
Location: Tread assembly area.
Project Specifics: Dense layout of production equipment, complex roof truss structure, difficult access to installation sites, and need to complete installation within 72 hours during a holiday.
Goal: To improve temperature conditions for machinery and staff and to prevent production shutdowns caused by overheating. To reduce VOC (volatile organic compound) concentrations and oil aerosols generated by rubber vulcanization.
Technology Used: 12 HVLS destratifiers: 8 units of FADS500WD + 4 units of FADS400WZ to enhance high-volume air circulation and disrupt temperature layering. Total energy balance: up to 10.0 kW. Air circulation volume: 2,840,000 m³/h.
Result: In summer, perceived temperature dropped by 4°C, and VOC concentration from manufacturing processes was diluted. In winter, destratification achieved by disrupting temperature layers helps save on heating costs.
2019: COOLING AND VENTILATION OF THE CVT1 PRESS AREA
Location: Large production hall for pressing bus and truck tires. Dimensions: 150 x 35 meters, ceiling height 9.5 meters. Winter temperatures reached 35°C, while summer temperatures hit 55°C, creating uncomfortable working conditions and affecting machinery reliability, especially in control panels, which often entered error modes, disrupting production and incurring service costs.
Project Specifics: Roof material and skylight structure required a side installation, involving custom-designed HVAC elements, support structures, and custom entry ducts. The original wired glass in the skylights where FAIRAIR technology was to be installed had to be replaced with modern dibond material.
Goal: To reduce the temperature below 50°C, prevent breakdowns in control systems, improve working conditions for staff, and maintain relative humidity below 60%.
Technology Used: Seven hybrid heat extractors (FAEP900) for intense extraction of heat load, exhaust gases, smoke, odors, and VOCs, plus seven adiabatic cooling units (FAEV601). Total energy balance: up to 12.5 kW; air exchange rate: 3.5x per hour.
Result: Temperature in winter dropped to 29°C from 35°C, and in summer to 35°C from 55°C.
2020: AIR BARRIER INSTALLATION
Location: Entrance to the main administrative building foyer, through which 500 people pass during each shift change.
Project Specifics: Integration of the air barrier unit into a design frame surrounding four entrance doors. Coordinated installation with the sliding door supplier. Extremely tight delivery deadline.
Goal: To completely separate the indoor and outdoor spaces, preventing cold air from entering the reception area and breaking strong drafts caused by the building’s open stairwell and long corridor behind the reception, which created rapid thermodynamic airflows.
Technology Used: Cold air barrier FBDS72, providing perfect separation of indoor and outdoor spaces with ∆T 1°C due to laminar airflow.
Result: Improved thermal comfort in the foyer; reception staff are no longer exposed to drafts, especially in winter.